Manufacturing Playbook
This playbook provides guidance to manufacturing and industrial firms located in Greater Des Moines (DSM).
Sample: Midsize Manufacturing Facility
The sample risk profile has been determined for a 100-employee manufacturing facility in DSM. The profile shows frequency, or how many people in a day; duration, or length of typical interaction; and variety, or the number of different people.*
The COVID-19 pandemic has hit manufacturers in unexpected and unprecedented ways. For the first time in modern manufacturing history, the critical variables of demand, supply and workforce are all impacted globally at the same time. Some companies that provide and deliver vital goods like personal care, paper and pharmaceutical are struggling to meet demand driven by panic buying. Others are experiencing dramatic drops in demand and extreme pressure to cut operational costs. Every major manufacturer is now experiencing disruptions across their supply chains of parts and raw materials, driven by what may now become recurring volatility of supply from South Asia. According to a survey by Fictiv, 95% of senior manufacturing decision makers reported that the pandemic has had long-term effects on their businesses. A large portion of that impact comes from supply chain problems, where 68% or respondents said that increasing supply chain resilience and agility is a top priority. To overcome the difficulties posed by COVID-19, 91% reported they have increased digital transformation investments in the past year while 77% reported that their increase was significant or dramatic.
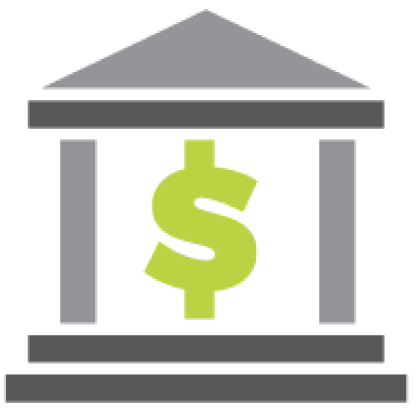
78% Anticipate
a Financial Impact
|
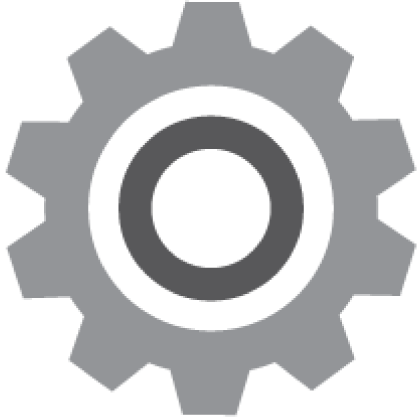
53% Anticipate
a Change in Operations
|
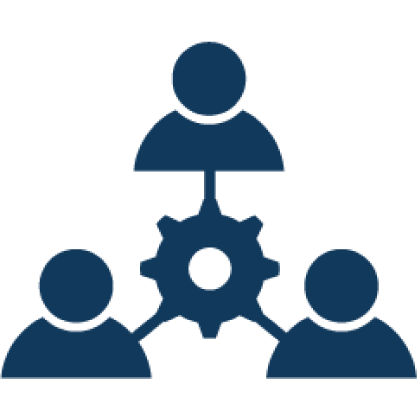
36% are Facing
Supply Chain Disruptions
|
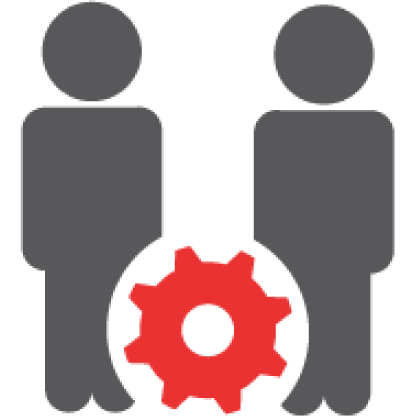
|
Supply Chain Resilience
Manufacturers must brace for disruptions to their supply chains. COVID-19 will impact supply sources and may slow down production once business volume returns. Manufacturers should consider a combination of centralized and decentralized supply options to adjust to external market conditions. Identifying alternative suppliers and robust communication and information sharing will accelerate this approach during COVID-19 and help prepare for disruptive events in the future.
|
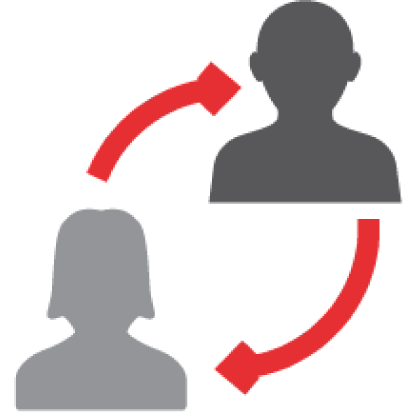
|
Change in Workforce Capabilities and Processes
Due to increased use of technology and generation of analytics, employees will need to learn how to leverage data to drive decision making in their facilities. Organizations should consider creating decentralized teams to react quickly to insights generated by advanced analytics, and leaders should adjust incentives to privilege learning and promote greater flexibility.
|
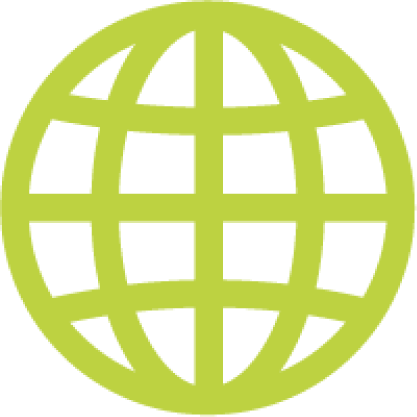
|
Enhanced Data and Technology
Organizations feel a greater sense of urgency to leverage automation and use of technology to improve collaboration, materials movement and optimize production. Organizations who employ analytical platforms and cloud-based tools will unlock insights from data and increase speed in decision making.
|
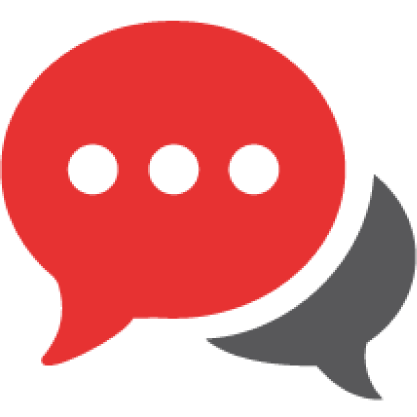
|
On-Demand Manufacturing
Instead of holding large quantities of products in storage facilities, manufacturers are increasingly setting production levels based on real-time customer demand as a way to minimize the impact of future supply chain disruptions. According to a survey by Fictiv, 84% of manufacturers have adopted on-demand manufacturing while citing increased quality, speed and production transparency as benefits.
|
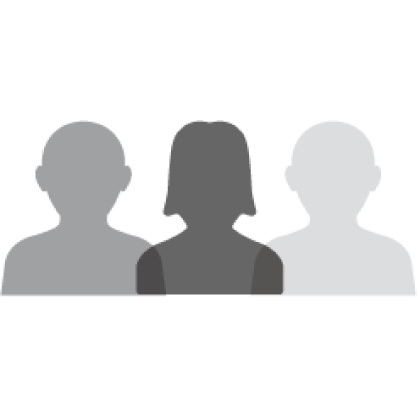
|
Increasing Employee Safety
Leverage tracking systems, heat mapping and monitoring devices to track the health and safety of workers. Companies, such as MakuSafe, of West Des Moines, monitor EHS data to mitigate workplace hazards and risk exposures for workers. Organizations should also seek ways to mitigate worker interaction by scheduled staggered shifts, deliberately routing human traffic in their faculties, creating physical barriers when possible and leveraging digital applications to conduct collaboration and planning offsite.
|
Health & Sanitation
- Conduct a health screening with all employees before their shifts in accordance with the most up-to-date recommendations from the local public health department.
- Encourage employees who feel sick to stay home. Employees who have had close contact with someone with COVID-19 should consult CDC guidance on when to self-quarantine.
- Face coverings and any other PPE should be worn by employees and members in accordance with the most up-to-date recommendations from the local public health department.
- Train all employees on cleaning processes, hand hygiene and respiratory etiquette.
- Provide tissues and no-touch trash receptacles for workers to use.
- Place handwashing stations or hand sanitizers with at least 60% alcohol in multiple locations to encourage hand hygiene. If possible, choose hand sanitizer stations that are touch-free.
- Clean high touch surfaces and shared objects once a day.
- You may want to either clean more frequently or choose to disinfect (in addition to cleaning) in shared spaces if certain conditions apply that can increase the risk of infection from touching surfaces:
- High transmission of COVID-19 in your community
- Low number of people wearing masks
- Infrequent hand hygiene
- The space is occupied by people at increased risk for severe illness from COVID-19
- If there has been a sick person or someone who tested positive for COVID-19 in your facility within the last 24 hours, you should clean AND disinfect the space.
- For tool-intensive operations, employers should ensure tools are regularly cleaned and disinfected, including at least as often as workers change workstations or move to a new set of tools.
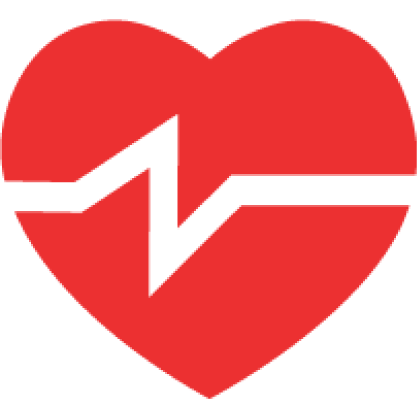
Workspace & Process
- Configure communal work environments so that workers are spaced at least six feet apart, if possible.
- Modify the alignment of workstations, including along production or assembly lines, if feasible, so that workers are at least six feet apart in all directions (e.g., side-to-side and when facing one another).
- Ideally, modify the alignment of workstations so that workers do not face one another.
- Encourage single-file movement with a six-foot distance between each worker through the facility, where possible.
- Consider using markings and signs to remind workers to maintain their location at their station away from each other and practice social distancing on breaks.
- Use physical barriers, such as strip curtains, plexiglass or similar materials or other impermeable dividers or partitions to separate manufacturing workers from each other, if feasible.
- Designate workers to monitor and facilitate distancing on production or assembly line floors.
- For some monitoring activities, it may be possible to leverage closed-circuit television (camera systems) to remotely view facilities as opposed to physically visiting the location.
- Add additional clock in/out stations, if possible, that are spaced apart, to reduce crowding in these areas.
- Stagger break times or provide temporary break areas and restrooms to avoid groups of workers during breaks. Workers should maintain at least six feet of distance from others at all times, including on breaks.
- Stagger workers’ arrival and departure times to avoid congregations of workers in parking areas, locker rooms and near time clocks.
- Remove or rearrange chairs and tables, or add partitions to tables in break rooms and other areas workers may frequent to increase worker separation. Identify alternative areas to accommodate overflow volumes such as training and conference rooms or using outside tents for break and lunch areas.
- Consider cohorts, or grouping together, of workers. This can increase the effectiveness of altering the plant’s normal shift schedules by making sure that groups of workers are always assigned to the same shifts with the same coworkers.
- Facilities should consider consulting with a heating, ventilation and air conditioning engineer to ensure adequate ventilation in work areas to help minimize workers’ potential exposures.
- If fans such as pedestal fans or hard-mounted fans are used in the facility, take steps to minimize air from fans blowing from one worker directly at another worker. Personal cooling fans should be removed from the workplace to reduce the potential spread of any airborne or aerosolized viruses. If fans are removed, employers should remain aware of, and take steps to prevent, heat hazards.
- Limit facility access only to essential workers.
- Encourage workers to avoid carpooling to and from work, if possible.
- If meetings must be held, such as at shift changes, break them into smaller groups instead of holding a larger meeting. Eliminate non-essential meetings.
- Have clear policies and HR practices that allow sick employees to stay home.
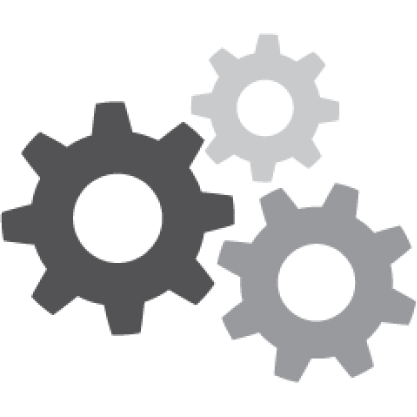
Communication
- Post signs and reminders at entrances and in strategic places providing instruction on social distancing, hand hygiene, use of cloth face coverings or masks and cough and sneeze etiquette.
- All communication and training should be accessible for people with disabilities, easy to understand and be provided in languages appropriate to the preferred languages spoken or read by the worker.
- Establish a system for employees to alert their supervisors if they are experiencing signs or symptoms of COVID-19 or if they have had recent close contact with a suspected or confirmed COVID-19 case.
Recommended Practices include preparedness checklist items developed by the Iowa State Center for Industrial Research and Service which can be found here.
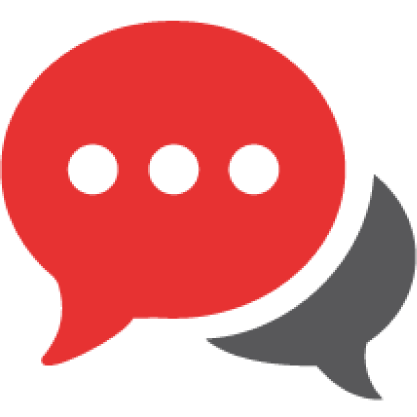
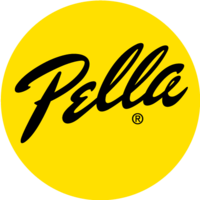
|
Producing Personal Protective Equipment (PPE)
Manufacturers offer unique capabilities in being able to quickly produce necessary equipment to protect frontline workers. Organizations who have created and donated PPE in DSM include Area 515, BDI Signs, Beeline and Blue, Corteva Agriscience, John Deere, Pella Corporation, Weiler, Nationwide, NCMIC and DMACC, among others.
|
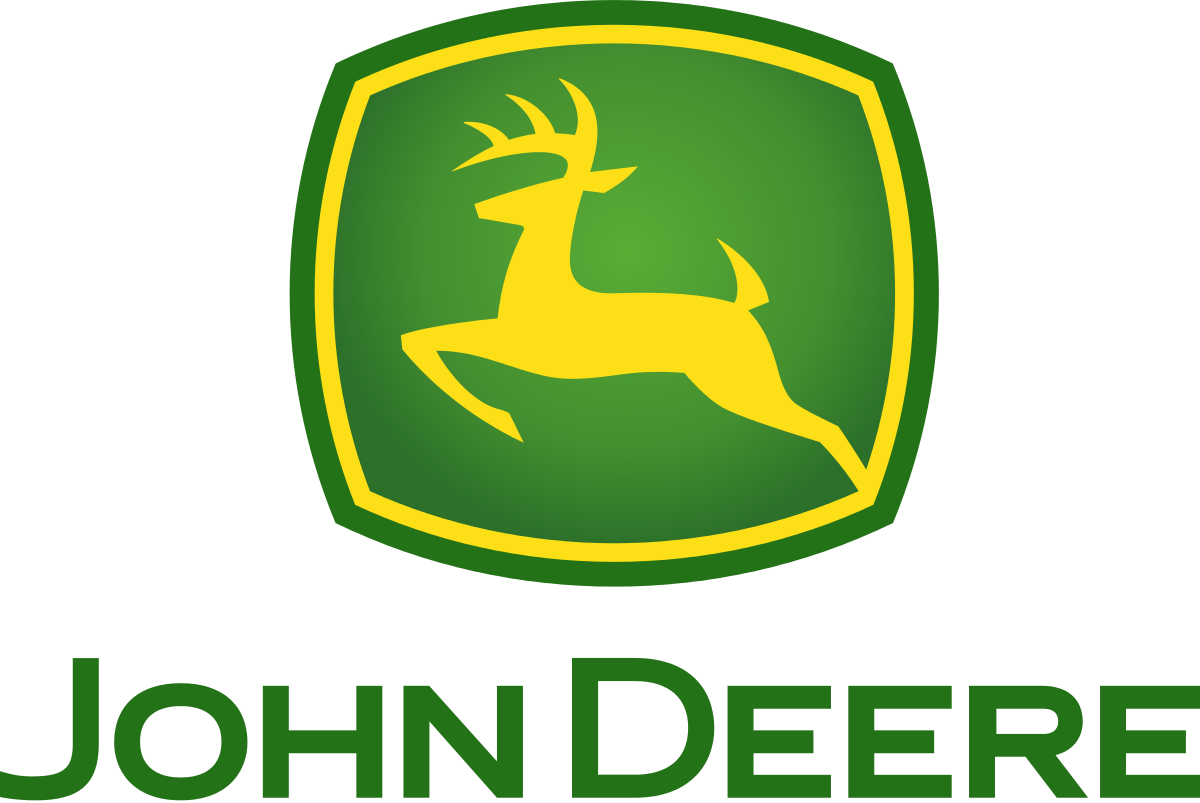
|
Partnering with Other Manufacturers to Support Essential
John Deere launched an Innovation Center and welcomes other manufacturers to use their blueprints, designs and templates in manufacturing products in their facilities for frontline workers and protecting their employees. Consider offering tools and resources for other manufacturers or partnering with other like-minded organizations.
|

|
Supporting Nonprofits
Consider supporting local nonprofits on the frontlines of COVID-19 and those impacted by the virus. In early April 2020, MidAmerican Energy donated $500,000 to over 30 local organizations including food banks, community foundations and United Way agencies.
|
Recommended Playbooks
The business function playbooks include takeaways that are specific to professional functions that could be present in any business, regardless of industry.
*We note that these assessments are qualitative and based on expert-led judgment (Johns Hopkins, 2020). Currently, there are not enough detailed data available to enable quantitative risk stratification. Businesses will need to make decisions about re-initiating business activities before there are validated data to know the precise levels of risk.
Legal Disclaimer
The Greater Des Moines Partnership's DSM Forward playbook is
not intended to constitute legal advice or provide specific direction. The preparation of a business continuity or preparations plan should be undertaken with the advice and direction of appropriate specialists and personnel, in consideration of the unique circumstances impacting each business. Third-party websites or material linked to or referenced in DSM Forward are for informational purposes only and do not constitute a recommendation of The Partnership of that material or its authors.
Last updated: 5/17/2021